Vol. 03, Issue 02 (2024): August-December
DOI:
10.53591/easi.v3i2.1867
ISSN-e:
2953-6634
Submitted:
October 30, 2024
Revised:
December 13, 2024
Accepted: January 8, 2025
Engineering
and Applied Sciences
in
Industry
University
of Guayaquil. Ecuador
Frequency/Year:
2
Web:
revistas.ug.edu.ec/index.php/easi
Email:
easi-publication.industrial@ug.edu.ec
How to cite
this article: Navarro, D. et al. (2024). Characterization of Fuels Obtained
from the Pyrolysis of Polystyrene. EASI: Engineering and Applied Sciences in
Industry, 3(2), 57-69. https://doi.org/10.53591/easi.v3i2.1866
Articles in journal repositories are freely open in
digital form. Authors can reproduce and distribute the work on any
non-commercial site and grant the journal the right of first publication with
the work simultaneously licensed under a CC BY-NC-ND 4.0.
Abstract. This study
addresses the specific characterization of fuels obtained through the pyrolysis
of polystyrene after being analyzed in laboratories and a study of their
applicability. Pyrolysis is the chemical decomposition of materials by
heating them at high temperatures without the presence of oxygen to decompose
them into simpler fractions. The research focused on evaluating viscosity,
flash point, density and ASTM distillation and then comparing the results with
commercial fuel standards. The results show that pyrolysis-derived fuels have
characteristics intermediate between diesel and gasoline, with a density
similar to diesel, but a viscosity and flash point closer to gasoline.
Distillation reveals a mixture of volatile and non-volatile components,
suggesting that these fuels could be alternatives, although further testing to
evaluate their performance and safety in specific applications is needed to
validate the feasibility and safety of polystyrene pyrolysis by-products as
alternative fuels.
Keywords:
Polystyrene, Pyrolysis, Fuels, Chemical Recycling, Plastics.
Resumen. Este estudio aborda la
caracterización específica de los combustibles obtenidos a partir
de la pirólisis del poliestireno después de haberlos analizado en
laboratorio y realizado un estudio de su aplicabilidad. La pirólisis es
la descomposición química de materiales calentándolos a
altas temperaturas sin presencia de oxígeno para descomponerlos en
fracciones más simples. La investigación se centra en la
evaluación de la viscosidad, el punto de inflamación, la densidad
y la destilación ASTM y Los resultados se compararon con los
estándares de combustible comerciales. Los resultados muestran que los
combustibles de pirólisis tienen características intermedias
entre la gasolina y el diésel, con una densidad similar al
diésel, pero una viscosidad y un punto de inflamación más
cercano al de la gasolina. La destilación revela una mezcla de
componentes volátiles y no volátiles, lo que sugiere que estos
combustibles pueden ser combustibles alternativos, incluso necesarios. Pruebas
adicionales para evaluar su rendimiento y seguridad en aplicaciones
específicas para validar la viabilidad y seguridad de los productos de
pirólisis de poliestireno como combustibles alternativos.
Palabras claves: Poliestireno,
Pirólisis, Combustibles, Reciclaje Químico, Plástico.o
1.
INTRODUCTION
Pyrolysis is a thermochemical reprocessing process that involves
heating plastics to high temperatures in the absence of oxygen, allowing their
decomposition into simpler compounds (Angulo & Carrera, 2023). By delving
deeper into the mechanisms involved in pyrolysis and conducting a thorough
characterization of the obtained products, the aim is to refine and optimize
this technique to produce more efficient and higher-quality fuels (Marimon,
2022).
The generation of fuels from the pyrolysis of
polystyrene is being developed in a context of growing concern about the
environmental impacts of plastics, driving the active search for innovative
technological solutions. Pyrolysis is considered a potential option to convert
plastic waste, such as polystyrene, into useful products like fuel. However,
despite its great potential, the comprehensive characterization of fuels
generated by this process remains an understudied but essential area to
evaluate the viability and sustainability of technology (Kwakwa & Alfonso,
2021).
Ecuador faces a significant challenge in managing
plastic waste, particularly single-use plastics. Managing this waste has become
an urgent necessity (Ortega et al., 2020) due to its slow degradation and the
severe environmental impacts it causes, such as air and water pollution
(Espinoza, 2022). In this context, the pyrolysis of polystyrene has emerged as
a potential alternative to address this problem, offering the possibility of
converting plastic into useful fuels and contributing at the national level (Castro
et al., 2024). This approach aims to transform plastic waste into value-added
products, significantly reducing its environmental impact and promoting more
sustainable resource management (Machado et al., 2015).
The study aimed to characterize the fuel extraction
process via pyrolysis to identify the optimal temperature and duration
conditions required to maximize liquid fuel production (Miandadd, 2017). The
resulting fuel may have a chemical composition different from conventional
fuel, making it necessary to conduct tests to evaluate its stability. These
tests may include engine performance analysis, emissions analysis, and
compatibility with current fuel systems (Pinargote & Sánchez, 2023).
1.1. Factors
that influence the pyrolysis of plastics.
The
efficiency of plastic pyrolysis is determined by several essential factors that
affect the yield and quality of the obtained products. These factors include:
Influence
of Temperature: Maintaining an
appropriate temperature is critical to initiating and sustaining the thermal
decomposition of polymers. Studies indicate that high temperatures can
accelerate the decomposition process and favor the production of gaseous and
liquid products with higher energy yield (Nuñez, 2019). However, at very
high levels, undesired byproducts such as dioxins and furans may be generated
(Mohamed, 2017).
Importance
of Residence Time: Residence time
determines the duration for which the input material remains in the reactor. A
longer residence period can facilitate a more complete decomposition of the
polymers and improve the generation of products of interest (Salinas & Vázquez,
2010).
Impact
of Pressure: Changes in pressure can
influence product distribution and the rate of chemical reactions. Research
shows that higher pressures can increase the production of gases and liquids,
while lower pressures favor the formation of solid carbon products (Rojas, 2012).
Composition
of Feedstock Material: The type of
plastic used in the pyrolysis process is another determining factor. Different
polymers have thermal and chemical properties that affect their decomposition
rate and the quality of the final products. Heterogeneous plastic mixtures may
require adjustments in operating conditions to maximize yield and minimize
unwanted byproducts.
1.2. Chemical
and physical properties of Commercial Diesel
API
Gravity: The specific gravity scale developed
by the American Petroleum Institute (API). This scale measures the relative
density of different petroleum-derived liquids, expressed in degrees. In
general, crude oil has an API gravity between 30 and 40 degrees, with
variations depending on its specific composition and the refining process it
has undergone (Maprin, 2022).
Specific
Gravity: The ratio between the absolute
density of a substance and that of a reference standard, which is water for
liquids and air for gases. The density of petroleum, also known as crude oil or
naphtha, ranges between 0.79 and 0.88 at a temperature of 15.6°C
(59°F), indicating it is less dense than water, which has a density of 1000
kg/m³.
PSW
(Water and Sediment Content): This parameter
is critical for evaluating fuel quality because it indicates the number of
impurities, such as sediments and water, present in the fuel. During
production, transportation, and storage, fuels can contain small amounts of
water. Excessive water can cause various problems.
ASTM
Diesel Distillation: This parameter is crucial
for assessing fuel quality, as it indicates the levels of impurities, such as
sediments and water, present in the fuel. Fuels may accumulate small amounts of
water during production, transportation, and storage, and excessive amounts can
lead to various issues.
Flash
Point: The minimum temperature at which a
flammable mixture can form when interacting with air. The Pensky-Martens
apparatus is used to determine this value. A flammable substance is one that
undergoes changes when in contact with fire or combustion. For diesel, the
flash point range is between 52°C and 96°C (INSST, 2018).
Kinematic
Viscosity: Secondary reference materials, such
as fuel oil No. 6 and diesel, were used with viscosities ranging from 347.0 to
869.5 mm²/s and colors between 0.5 and 7.9 units. Precision parameters and
uncertainty were evaluated and analyzed. Certified reference materials (N600)
were used to verify accuracy.
Sulfur
Content: To meet the demand for premium oil in
Ecuador, the Esmeraldas refinery produced this type of oil with an average
sulfur content of 44 ppm in February 2022, representing about 35% of the
national supply of hydrocarbons (EP PETROECUADOR, 2022).
ASTM
Color: This system, known as the "mineral
oil color value," classifies petroleum-derived products. During the
refining process, the color of mineral oils is continuously monitored to ensure
they are refined to the appropriate level. Additionally, it helps ensure proper
fuel use for its intended purpose and prevents contamination and quality
degradation (Hernández, 2009).
Calorific
Value: In diesel engines, 7% to 10% biodiesel
is used. This is added to diesel to reduce soot production during combustion
and improve the calorific value. The higher the temperature in the combustion
chamber, the more fuel can be burned, reducing the effort required to move the
piston and connecting rod within the engine. The lower calorific value of
biodiesel is 35.86 MJ, although it can vary depending on its composition (RACE,
2022).
2.
MATERIALS AND METHODS
An exploratory study was conducted to analyze the chemical and physical
properties of fuel derived from plastic pyrolysis. Using a qualitative and
quantitative approach, a laboratory analysis was carried out to identify its
properties and potential applications.
2.1.
Acquisition of raw
material
For the
pyrolysis sampling, 1 kg of granulated polystyrene is weighed and placed into
the reactor, after which the flange is securely closed. Water is then
introduced into the condenser, maintaining a temperature of 1 to 3°C. Over
approximately 6 to 7 minutes, polymerization reactions occur within the
reactor, as illustrated in Figure 1. At the end of the process, the pyrolysis
product is collected in a 1L container, which is subsequently transported to
the laboratory for critical analysis.
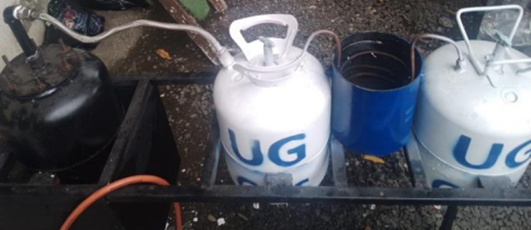
Figure
1. Preparation for Pyrolysis. Source: The Authors (2024)
.
2.2. Laboratory characterization test
Once
the liquid sample was obtained through the pyrolysis process, various
characterization tests were conducted in the laboratory using 1 liter of the sample.
These tests were designed to analyze key properties of the generated fuel and
assess its potential applicability. The methods used are described below:
API
Gravity
The
API gravity was measured using a 1-liter graduated cylinder filled with the
liquid sample. A hydrometer was used to record the corresponding value after
stabilization, and the result was then adjusted to the reference temperature
using standard tables. The final value was calculated based on these
adjustments to ensure consistency with petroleum measurement standards.
Specific
Gravity
The
specific gravity was calculated using the standard formula based on API
degrees, providing a precise value under controlled conditions. The calculation
was performed using the following equation:
(1)
Where:
API: Degrees API 15,6 °C
SG: Specific gravity
Water and sediment Content (PSW)
The
water and sediment content were determined following the NTE INEN 1494
standard. A 50 ml sample and 50 ml of solvent were prepared in two centrifuge
tubes, ensuring that both tubes had equal volumes. The tubes were then sealed
with stoppers and mixed thoroughly. They were placed in a centrifuge set at
140°F (60°C) for 15 minutes at 1300 rpm.
ASTM Distillation
To perform
the distillation of the pyrolytic liquid derived from polystyrene, 1 liter of
the sample was introduced into the distillation flask (Figure 2). As the
temperature increased, the distilled liquid was collected in a graduated
cylinder. The resulting temperature and volume data were recorded to construct
the ASTM distillation curve
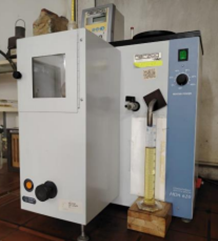
Figure 2. Representation
of the ASTM Distillation Curve. Source: The Authors (2024)
Flash point
The flash point was estimated by filling the Cleveland
cup with the liquid sample until the meniscus reached the reference mark. The
sample was then heated at a rate of 2°C per minute while the flame was
brought closer in a steady and uniform motion.
Kinematic Viscosity at 40°C
To measure the kinematic viscosity, 20 liters of
distilled water were used. First, the time required for a specific volume of
liquid to flow by gravity through a capillary tube into the viscometer was
measured, ensuring a constant temperature of 40°C. The viscosity constant
was then multiplied by the recorded time to obtain the viscosity value.
Color Analysis
The color analysis was performed by comparing the
sample with standard patterns using a colorimeter. This allowed the evaluation
of the liquid's purity and the detection of possible contaminants. Each of
these tests contributed to the comprehensive characterization of the obtained
product, providing essential data for its comparison with conventional fuels
and for assessing its feasibility in practical applications.
2.2
Polystyrene (PS) pyrolysis processes in the laboratory
To identify
the optimal parameters for the pyrolysis process, several tests were conducted
at different operating temperatures: 300°C, 350°C, and 400°C, using
a specialized laboratory reactor. These tests help determine which conditions
yield the best performance. In each test, 100 g of polystyrene was weighed and
introduced into the reactor, which was maintained at the desired temperature
for 60 minutes. At the end of the process, the reactor was allowed to cool
before the solid residue was extracted and weighed. The final mass was recorded
to calculate the process yield in terms of the percentage of residual mass.
This experimental approach facilitates the adjustment and improvement of the
process to ensure maximum efficiency under real operating conditions.
Additionally, by analyzing how yield varies with temperature, potential issues
during process scaling can be predicted and resolved, ensuring its robustness
and effectiveness in high-speed implementation.
Determination of Pyrolysis Parameters at Laboratory
Scale
Below are
the experimental data obtained at temperatures of 300°C, 350°C, and
400°C. These results provide information about the properties and behavior
of materials exposed to different pyrolysis temperatures.
Test
1 - Analysis at 300 °C
The tests
were conducted at a constant temperature of 300°C, using an initial mass of
110 g. The liquid volumes obtained showed slight variations, with recorded
values of 82, 85, and 80 ml, averaging 82.3 ml and a standard deviation of 2.5
ml. The liquid density remained stable at 0.903 g/ml. The liquid mass ranged
from 72.3 g, 79.4 g, and 75.9 g, with an average of 75.86 g and a standard
deviation of 2.2 g. For the solid product, the generated mass fluctuated
between 11.3 g, 14.6 g, and 14.5 g, with an average of 13.46 g and a standard
deviation of 1.7 g. Finally, the gas mass produced varied between 12.7 g, 9.7
g, and 14.3 g, with an average of 12.23 g and a standard deviation of 2.9 g.
Test
2 - Analysis at 350°C
The
experiments at 350°C showed liquid volumes ranging from 107, 109, and 104
ml, with an average of 106.66 ml. The liquid density remained constant at 0.908
g/ml. The liquid mass obtained fluctuated between 92.5 g, 98.4 g, and 90.7 g,
giving an average of 93.86 g and a standard deviation of 2.1 g. Regarding the
solid product, the generated mass varied between 5.3 g, 2.6 g, and 6.5 g, with
an average of 4.8 g and a standard deviation of 1.2 g. Finally, the gas mass
produced ranged between 3.5 g, 2.9 g, and 4.3 g, with an average of 3.56 g and
a standard deviation of 1.0 g.
Test
3 - Analysis at 400 °C
Under
conditions of 400°C, the liquid volumes obtained ranged from 109, 111, and
106 ml, with an average of 108.66 ml. The liquid density remained around 0.910
g/ml. The liquid mass varied between 97.4 g, 99.6 g, and 91.2 g, with an
average of 96.06 g and a standard deviation of 1.9 g. Regarding the solid
product, the generated mass ranged from 4.7 g, 3.0 g, and 5.1 g, with an
average of 4.26 g and a standard deviation of 1 g. The gas mass produced varied
between 0.4 g, 0.7 g, and 3.5 g, with an average of 1.53 g and a standard
deviation of 1.1 g.
3.
RESULTS AND DISCUSSION
The
different performances obtained during the tests are shown in Figure 3. This
graph provides a clear visual comparison of how different conditions affect the
process performance.
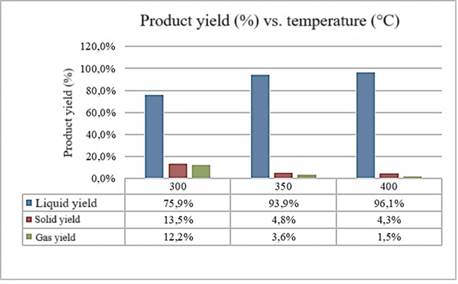
Figure 3. Performance
at different temperatures. Source: Prepared by the authors (2024).
Table 1
summarizes the data from each pyrolysis process, used for a general
characterization of the process, utilizing the average values obtained. It
includes variables and results for each test, facilitating comparative analysis
and the identification of patterns for a more detailed and accurate
understanding of the process behavior under different experimental conditions.
Table 1. Pyrolysis process conditions
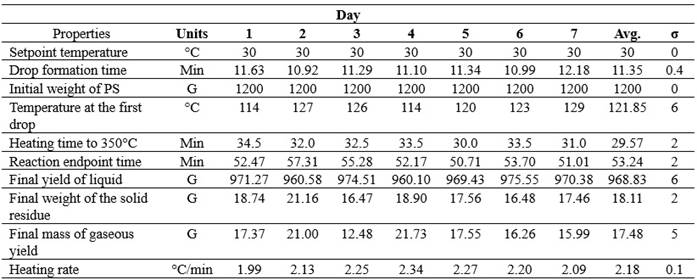
Source: Prepared by the authors (2024).
During the experiment, the initial temperature and initial weight of
the PS remained constant on all test days, without any change in these initial
conditions.
The curves presented in Figure 4 show a detailed picture of how the
temperature changes with time during the pyrolysis process in each case
examined.
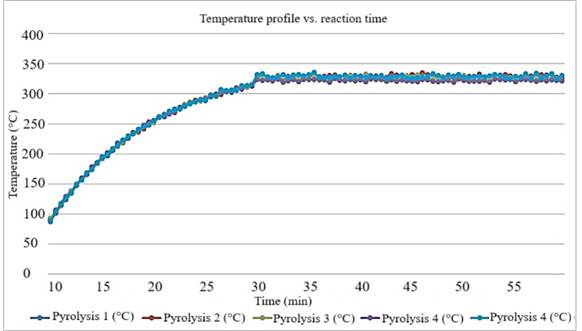
Figure 4. Profile Temperature in Pyrolysis tests VS reaction time.
Source: Prepared by the authors (2024).
Figure 5 shows the results of the mass balance of
the products generated in the pyrolysis process, expressed in percentages.
Details how final products are distributed based on their mass.
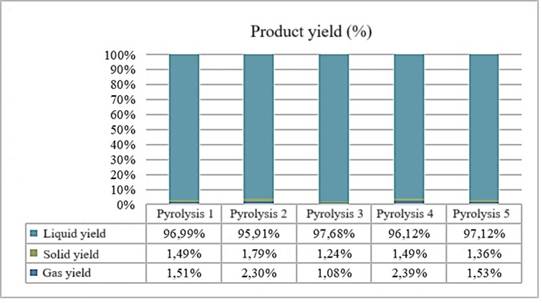
Figure 5. Efficiencies of each Pyrolysis. Source: Prepared by the authors (2024).
The amount of alternative fuel produced from the
collected polystyrene is estimated, we find that around 10.2 L of this fuel are
produced per day and the monthly production is approximately 225L.
3.1
Distillation of the Alternative Fuel
ASMT Distillation
The results obtained show variability but remain stable
in terms of recovery percentage, residues, and losses during distillation. The
recovery percentage ranged from 80% to 85%, suggesting reasonable consistency
in product recovery. Residue percentage ranged from 15% to 19%, reflecting
slight differences in the amount of residue left after the process.
Losses remained low, with values between 0% and 1%,
indicating good control of losses during distillation. Regarding characteristic
boiling points (BWP), the results showed greater variability. The initial
boiling point (IBP) ranged between 127°C and 135°C. Boiling points at
percentiles (10%, 50%) and the final boiling point exhibited variations, with
averages of 137.5°C, 147.6°C, and 275°C, respectively, and adjusted
standard deviations of 0.5°C.
The data in Table 2 detail the basic properties
obtained from five steps of the second distillation of the product derived from
the first distillation of the pyrolytic oil. Losses were low, ranging from 0%
to 1%, with an average of 0.45%, suggesting effective control of these losses.
Table 2. Estimation of Fuel Generated from Recycled PS
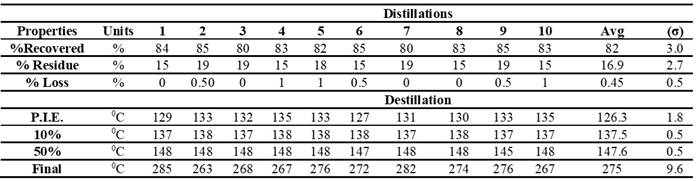
Source: Prepared by the
authors (2024).
To evaluate the composition and thermal properties
of the product compared to traditional fuels such as diesel and gasoline, it is
crucial to compare the ASTM distillation curve of the liquid product with the
distillation curves of diesel and gasoline. This comparison can be observed in
Figure 6. The graph highlights significant similarities and differences between
the distillation profiles of each substance.
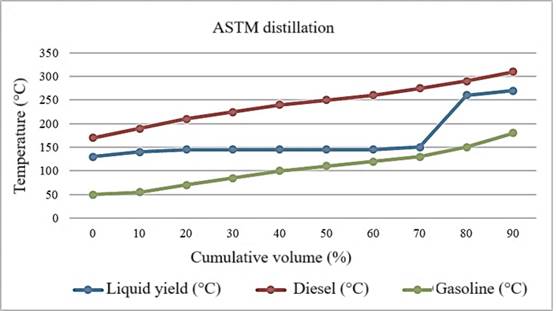
Figure 6. Comparison of ASTM Distillation Curves. Source: Prepared by the
authors (2024).
3.2 Characterization
tests
API
and Specific Gravity
A comprehensive API density analysis and adjusted
specific gravity calculations were performed for each pyrolysis test. These
data are essential for understanding the physical and chemical properties of
the product created during this thermochemical process. The API gravity
measures the relative density of liquid hydrocarbons compared to water,
providing key information about their specific density and ability to float or
sink. Specific gravity, corrected to a standard temperature, allows for
consistent comparisons between different samples.
Table 3 presents the API gravity and specific gravity values of the product
obtained at different temperatures. The API gravity results at 28°C range
from 21 to 21.6, indicating considerable stability in relative density compared
to water at this standard temperature. On the other hand, the API gravity at
15.6°C ranges from 19.34 to 21.14, suggesting greater variability in
density at lower temperatures, affecting properties such as fluid behavior.
Specific gravity, also calculated at 15.6°C, shows consistently close
values, highlighting high precision and stability in measuring the product's
density.
Table 3. API Gravity and Specific Gravity of the Product

Source:
Prepared by the authors (2024).
Kinematic
viscosity measured at 40°C
The kinematic viscosity values obtained at 40°C
allow for an analysis of the fluid's flow behavior under specific conditions,
providing key information about its performance in industrial and commercial
applications. These results reveal notable differences between the initial
liquid product and the distillates obtained. Table 4 shows that the liquid
product has higher viscosity values. In comparison, distillates 1 and 2 exhibit
lower viscosities and reduced standard deviations, reflecting their improved
fluidity.
Table
4. Kinematic Viscosity Results.
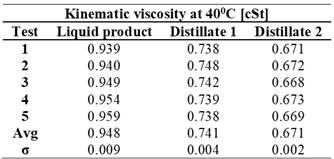
Source: Prepared by the
authors (2024).
Flash Point
The flash point, a crucial property for evaluating fuel safety and
handling, was analyzed using the Cleveland open cup method. The liquid sample
was poured into the container up to the reference mark and heated at a constant
rate of approximately 2°C per minute. During heating, a test flame was
uniformly applied until the moment when the emitted vapors formed a flammable
mixture upon contact with air.
The results indicated that the initial fuel had a
flash point range between 34°C and 39°C, with an average of 37°C
(Table 5). In contrast, the distillates obtained after the refining process
showed lower values: the first distillate averaged 35°C, while the second
recorded 32°C. This suggests that the distillation process not only affects
the chemical composition but also the product's volatility, making the
distillates more susceptible to ignition compared to the original liquid.
Table
5. Kinematic viscosity results
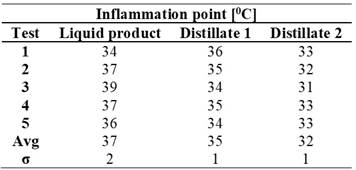
Source: Prepared by the authors (2024).
Water
and Sediment Content
The water and sediment content in the liquid product
was evaluated to determine its purity and potential impact on practical
applications. The analysis was conducted following established standards, using
a centrifugation procedure. Two 50 ml samples were prepared and combined with
an appropriate solvent in centrifuge tubes. After agitating the samples to
ensure a homogeneous mixture, the tubes were centrifuged at 1300 rpm and
60°C for 15 minutes.
The results indicated that the total water and
sediment content in the liquid fuel was less than 0.05%. This low concentration
of impurities enhances fuel performance by reducing the risk of clogging in
injection systems and minimizing wear on mechanical components.
In additional tests, the distillate obtained was
blended with diesel in proportions of 9.5% and 90.5%, respectively. This
mixture met technical specifications, achieving a flash point of 56.3°C.
This value, higher than the flash point of the initial liquid product,
represents an improvement in fuel safety during storage and handling, as it
reduces the risk of fires or explosions. The low proportion of sediment and
water also ensures more efficient performance in combustion engines.
ASTM
Color
The ASTM color analysis revealed that the first
distillate has a value of 1.5 ASTM units, while the second distillate registers
a value below 0.5 ASTM units. These results indicate that the second
distillation is significantly cleaner than the first, suggesting higher purity
and a lower presence of impurities or contaminants. This is advantageous for applications requiring
high-quality fuels.
3.3
Comparison of Results with Other Fuels
The results of the comparison, detailed in Table 6, show clear differences in several key properties
between the original liquid product and the two distillates obtained. The
viscosity of the liquid product is 0.948 cSt, whereas distillates 1 and 2 have
lower viscosities of 0.741 cSt and 0.671 cSt, respectively. These differences
suggest that the distillation process reduces flow resistance, potentially
making the product easier to handle in various applications.
Table
6. Comparison of Fuel Products.
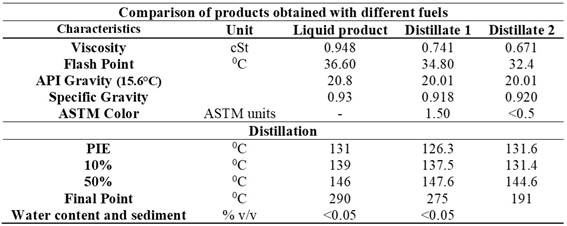
Source:
Prepared by the authors (2024).
3.4
Comparison of the Sample with Commercial Fuel Properties
Comparative
Analysis of API Gravity
API
gravity, which measures the relative density of liquid fuels compared to water,
is a fundamental parameter for evaluating their performance in practical
applications. In this study, the API gravity values of the pyrolysis products
were compared with the standards of traditional fuels like diesel and gasoline.
The
results show that gasoline, with an API gravity of 55.30°C, is
significantly less dense than diesel, which has an average of 35.34°C. In
contrast, the liquid product from pyrolysis has a much higher density, with an
average API gravity of 20.8°C. The distillates obtained from the process
show similar values, around 20.01°C.
These
differences indicate that fuels obtained through pyrolysis are denser than
conventional commercial fuels. This suggests that they may have a higher energy
content per unit volume, although they could also influence certain combustion
characteristics. The API gravity analysis highlights that these products
possess distinctive physical properties that must be considered when evaluating
their viability as alternative fuels or additives in blends with other
hydrocarbons.
Comparative
Analysis of Specific Gravity
The density values obtained from pyrolysis were
compared with standard values for diesel and gasoline fuels. Diesel has a
specific gravity of 0.835, while gasoline has a specific gravity of 0.74. In
contrast, the liquid pyrolysis product has a density of 0.93, and distillates 1
and 2 have values of 0.918 and 0.92, respectively.
Specific gravity measures the relative density of a
liquid compared to water, where higher values indicate greater density.
Gasoline, with a density of 0.74, is less dense than diesel, at 0.835. On the
other hand, the liquid products obtained through pyrolysis have higher density
values (0.93 for the liquid product and between 0.918 and 0.92 for distillates
1 and 2), indicating they are denser than conventional fuels.
The pyrolysis product has a higher density than the
two fuels mentioned. Regarding its potential use compared to the commercial
fuels listed in the table, if the pyrolysis product exhibits other suitable
properties, such as viscosity, flash point, and energy content similar to those
fuels, its use can be considered as a fuel or additive. However, its higher
density may reflect differences in combustion characteristics or energy
content, which should be considered when evaluating its feasibility as an alternative
commercial fuel.
The viscosity results of the pyrolysis product are
compared with the typical values for diesel and gasoline fuels. The kinematic
viscosity of diesel generally ranges from 2.0 to 4.5 cSt, while that of
gasoline is significantly lower, between 0.6 and 0.9 cSt. In comparison, the
liquid products obtained from pyrolysis have viscosities of 0.948 cSt for the
liquid product and 0.741 cSt and 0.671 cSt for distillates 1 and 2,
respectively.
Viscosity is a key parameter for determining the
flow and fluidity of a fuel. It has been found that diesel has a moderate
viscosity, while gasoline is significantly less viscous. The products obtained
from pyrolysis have a viscosity lower than that of diesel but slightly higher
than that of gasoline. This suggests that they may be suitable for some
industrial and commercial applications.
Comparative Flash
Point Analysis
The
flash point results are compared with typical values for fuels such as diesel
and gasoline. In general, diesel has a flash point of around 74°C, while
gasoline has a much lower flash point, around 48.5°C. The liquid products
obtained from pyrolysis have flash points of 36.6°C for the liquid product
and 34.8°C and 32.4°C for distillates 1 and 2, respectively.
The
flash point is crucial for determining the minimum temperature at which a
liquid can emit enough vapor to form a flammable mixture with air. Diesel has a
higher flash point, indicating greater resistance to ignition compared to
gasoline. At the same time, pyrolysis products have lower flash points than
diesel but slightly higher than gasoline, suggesting lower resistance to
ignition.
Comparative ASTM
Distillation Analysis
The
comparative ASTM distillation analysis reveals how the pyrolysis results align
with typical distillation values for diesel and gasoline. According to Table 7,
diesel has higher initial and final points (PIE: 145°C, final point:
360°C) compared to gasoline (PIE: 87°C, final point: 215°C),
indicating a higher percentage of heavier components.
On the other
hand, the pyrolysis products have initial and final points (PIE: 131°C,
final point: 290°C) lower than diesel but slightly higher than gasoline,
suggesting a lighter composition.
Table 7. ASTM Distillation Comparison of Pyrolysis Product
with Commercial Fuels like Diesel and Gasoline
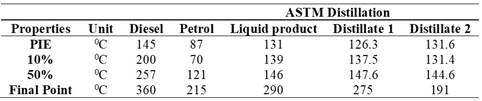
Source: Producted by the authors (2024).
CONCLUSIONS
The data from the analyses reveal a clear
relationship between the pyrolysis temperature and the process yield. At 300°C,
a yield of 85% was achieved, indicating that a large portion of the polystyrene
was converted into pyrolysis products. This high yield suggests that the
pyrolysis process is effective in the initial breakdown of polystyrene at
relatively low temperatures. However, when the temperature increases to
350°C, the process yield drops to 80%. This reduction could be associated
with the volatilization of intermediate products generated during pyrolysis,
which are lost as gases or vapors at higher temperatures.
The loss of these volatile compounds may result in a
greater mass loss, negatively affecting the overall yield of the process. When
the temperature increases to 400°C, the process yield further decreases to
75%. This decline indicates that, at higher temperatures, polystyrene
decomposes more completely, producing a greater amount of gases and liquids
that are lost. Although the conversion of the material is more thorough, the
greater mass loss can reduce the process efficiency in terms of producing recoverable
solids.
Polystyrene pyrolysis proves to be an effective
method for converting plastics into fuels, though its efficiency varies with
the operating temperature. At lower temperatures, the yield is higher, while at
higher temperatures, mass loss increases, suggesting the need to adjust and
optimize process conditions. The characteristics of the produced fuel vary
according to the pyrolysis temperature, influencing its fluidity and stability.
At lower temperatures, the fuel tends to be lighter and more fluid, while at
higher temperatures, the viscosity increases, which may limit its use in some
applications.
Polystyrene pyrolysis could be a viable alternative
for plastic waste management and fuel generation.
REFERENCES
Angulo & Carrera (2023) Obtención De Combustible
Líquido, Mediante El Proceso De Pirólisis A Partir De Residuos
Plásticos. Universidad Politécnica Salesiana. https://dspace.ups.edu.ec/bitstream/123456789/26153/1/UPS-GT004648.pdf
Castro,
P. (2024, noviembre 12) Energy policy implications of Ecuador´s NDC.
Journal of Infrastructure, Policy and Development 2024, 8(13), 7542. https://doi.org/10.24294/jipd7542
EP PETROECUADOR. (2022, marzo 25). https://www.eppetroecuador.ec/?p=12532#:~:text=Para%20abastecer%20la%20demanda%20de,de%20hidrocarburos%20a%20escala%20nacional
Espinoza, S. (2022) Energy Transition Scenarios for Fossil
Fuel Rich Developing Countries under Constraints on Oil Availability: The Case
of Ecuador. Energies. https://doi.org/10.3390/en15196938
Hernández, C. (2009, enero). https://www.scielo.org.mx/scielo.php?script=sci_arttext&pid=S1405-77432012000300004
INSST (2018). Fichas Internacionales de Seguridad
Química (ICSCs). https://chemicalsafety.ilo.org/
Kwakwa, V., & Alfonso, G. (2021, abril 6). Banco
Mundial Blogs. https://blogs.worldbank.org/es/voices/residuos-plasticos-crecienteamenaza-y-oportunidad-desperdiciada
Machado, P. Araujo, M. Torres, L. Oliveira, J. Walter, A.
(2015, abril 5). The use of
socioeconomic indicators to assess the impacts of sugarcane production in
Brazil. Renewable and Sustainable Energy Reviews. Volume 52, December 2015,
Pages 1519-1526. https://doi.org/10.1016/j.rser.2015.07.127
Marimon, K. J. (2022). Universidad Antonio Nariño. https://repositorio.uan.edu.co/server/api/core/bitstreams/f1634e9a-9111-43ec-a0d6-7b3ae195cf48/content
Miandad, B. (2017). Effect of plastic waste types on
pyrolysis liquid oil. International Biodeterioration and Biodegradation, 119,
239–252.
Mohamed. (2017). Fourier Transform Infrared (FTIR)
Spectroscopy. https://www.sciencedirect.com/science/article/pii/B9780444637765000012
Nuñez, N. (2019). Escuela Superior
Politécnica de Chimborazo. http://dspace.espoch.edu.ec/bitstream/123456789/13104/1/96T00552.pdf
Ortega-Pacheco, D. (2021) Social and Economic Contribution
of the Bioeconomic Sector in Ecuador: A Methodological Approach. https://doi.org/10.1007/978-981-15-7321-7_3
Pinargote Bravo, L., & Sánchez Muñoz, Y.
(2023, febrero). Escuela Superior Politécnica.
RACE. (2022, septiembre 28). https://www.race.es/poder-calorifico-y-otroscombustibles
Rojas, A. (2012). Efecto de la velocidad de calentamiento y
la biomasa en la cinética. http://bdigital.unal.edu.co/51518/7/9789587610321.pdf
Salinas, V., & Vázquez, F. (2010). Diseño
y construcción de un sistema de combustión para la
caracterización térmica de desechos plásticos utilizados
como combustible alternativo. Sangolquí.